Don't see what you are looking for? Many other
products available. Please use our
quickquote form to inquire.
These seals are used today around the world for a wide
variety of static and dynamic sealing applications.
The four-lobed design provides twice the sealing surface
of a comparable standard o-ring and because of this
double-seal action, less squeeze is required to maintain
an effective seal. This reduction in squeeze means less
friction and therefore, improved seal life.
Unlike o-rings, where parting lines are on the sealing
surface, QUAD-RING seals' parting lines lie between the
lobes, away from the sealing surface. This design
eliminates the problems of leakage often resulting from
a parting line's irregular surface.
QUAD-RING seals can be used as compression-type seals in
high speed rotary applications, eliminating the need for
costlier spring-loaded seals. They offer low friction
for long life in hydraulic systems with speeds of up to
900 FPM (4.5 M/Sec).
|
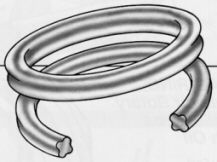 |
|
|
In order to minimize breakaway friction, an o-ring groove
must be wide enough to allow rolling or twisting of the
seal. In the long stroke of a reciprocating seal
application, this twisting action can strain and finally
rupture the rubber, resulting in a type of seal failure
known as spiral twist
The QUAD-RING seal's four-lobed configuration is designed to
withstand the distortion and extrusion often caused by high
or pulsating pressure, and thus eliminates this rolling
action. As a result, a QUAD-RING seal calls for a narrower
groove cross-section than does a comparable o-ring seal.
The following sections are guidelines for the design of
QUAD-RING seal grooves for both rotary and non-rotary
applications. |
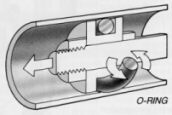
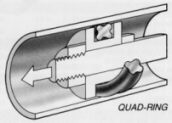 |
|
|
|
Information Provided by Minnesota Rubber/Quadion Corporation, copyright
2002
Product names are
Registered trademarks of Minnesota Rubber, A Quadion Company.
|